PB-series
Reliable and easy to maintain
PB-series rotary vane compressor VSD
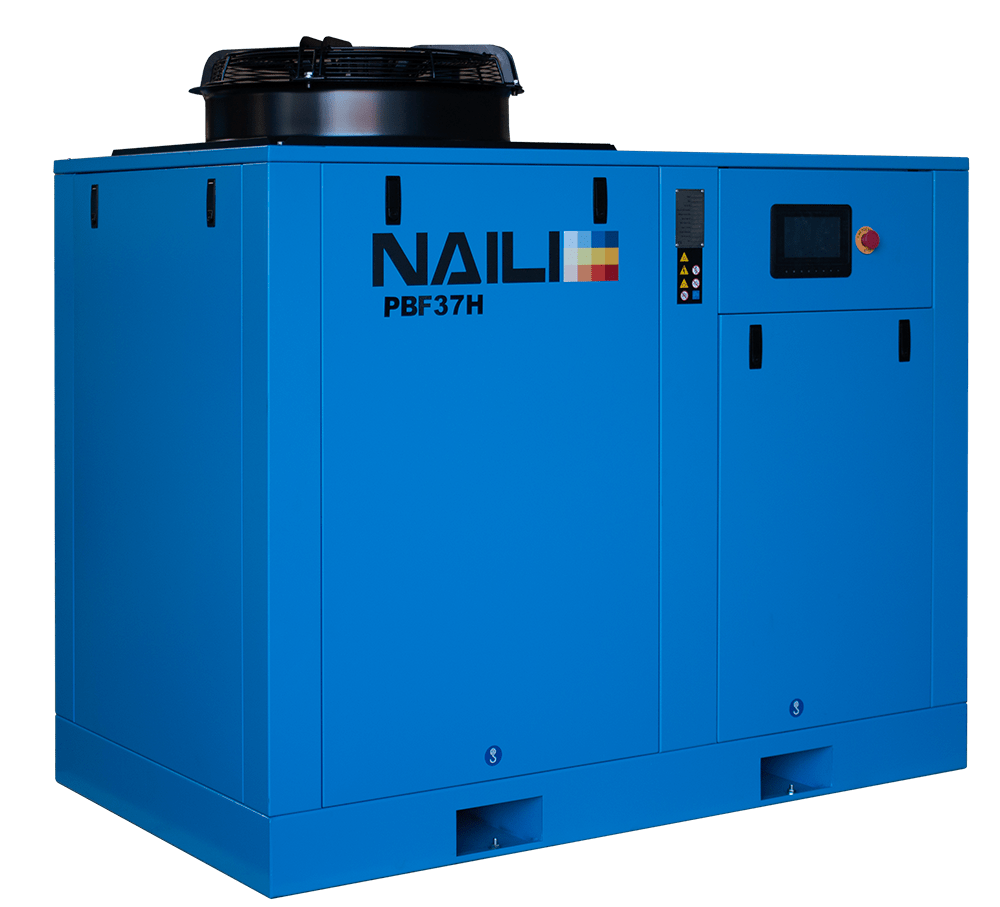
The PB-series is equipped with a sound-insulating cabinet, making the compressor very quiet in use. You can therefore position the compressor close to a workplace, in accordance with occupational health and safety regulations. The frequency controller ensures optimum energy use.
These compressors have a simple control that supports the user during use. You have the option to set up each compressor in cascade (max. 16) with this control. In this way you achieve the desired air output and you observe the correct load per machine.
The temperature of the outgoing compressed air is approx. 10 °C above ambient temperature thanks to the large radiator. This makes it possible to connect the compressor directly with a compressed air dryer, before storing the compressed air in a tank.
Because a rotary vane compressor has few parts subject to wear, the maintenance of this machine is minimal when compared to other techniques.
With a Naili rotary vane compressor from the PB-series, you have a very reliable, maintenance-friendly and low noise compressor, suitable for a long service life.
The PB series is available in 8 – 10 – 13 bar versions
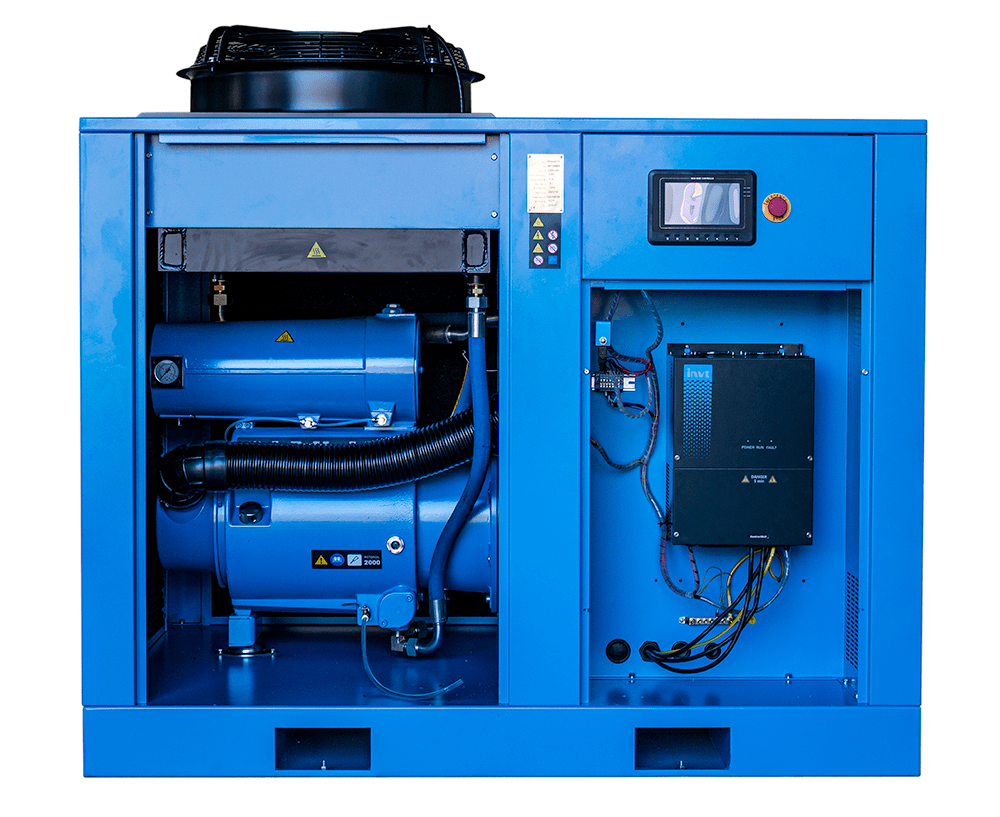
Oil separator
The oil separator ensures that only
5 ppm oil residues are carried
in the compressed air produced.
Airend
The airend is the heart of the compressor.
The rotor with which the compressed air is
generated is connected in-line with the
electric motor. This is the most efficient
way of energy transfer.
Motor
The electric motor is connected in-line
to the rotor in the airend. This is the most
efficient way of energy transfer. Naili uses
IE3 and IE4 motors.
Display
The easy-to-operate displays
allow the user to read or set
the status of the compressor
quickly and effectively. Cascading
or remote control are included
in every control as a standard.
Fan
The fan ensures that the compressoroil
is cooled properly. This fan also ensures
that the compressed air leaves the
compressor at ambient temperature +10°C.
As a result, other subcooling is not required
to get the compressed air ready for drying
and filtration.
Cover closing clips
The quick-release fasteners allow
the soundproof enclosure to be easily
removed for efficient maintenance.
Electrical junction box
The supply voltage can be easily
connected in the housing by means
of a cable gland. Optionally, the
frequency converter is also positioned
here.
Frequency converter
The frequency converter provides
a lower motorspeed when 100%
capacity is not requested. This saves
considerably on the energy consumption.
Assemble item code
Naili | NA | ||||||||
Series | PB | ||||||||
kW | 7.5 | 11 | 15 | 18.5 | 22 | 30 | 37 | 45 | 55 |
Bar | 8 | 10 | 13 |
Flow rate in m³/min
8 bar | 10 bar | 13 bar | |
---|---|---|---|
7.5 kW | 1.41 | 1.17 | 0.96 |
11 kW | 1.96 | 1.71 | 1.33 |
15 kW | 2.71 | 2.21 | 1.85 |
18,5 kW | 3.29 | 2.65 | 2.25 |
22 kW | 3.76 | 3.21 | 2.56 |
30 kW | 5.68 | 4.72 | 3.71 |
37 kW | 6.90 | 5.74 | 4.77 |
45 kW | 8.37 | 7.10 | 5.92 |
55 kW | 9.14 | 9.03 | 7.11 |
Additional energy saving and backup
Cascade setup
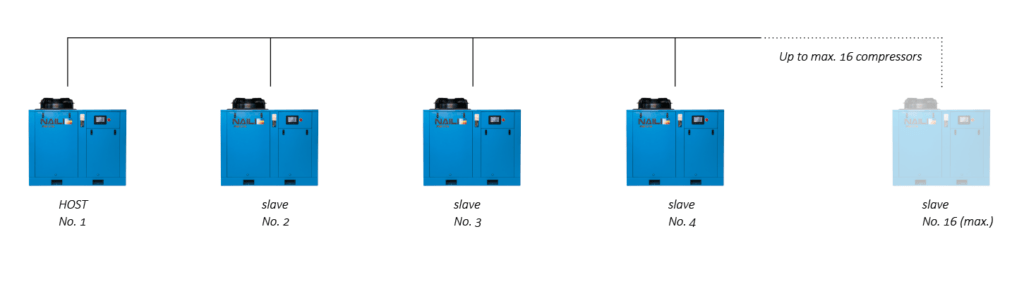
It is cost-effective to connect several compressors in a communicating setup. Therefore it is important to understand what volume and pressure of compressed air is required in a certain period of time. Always have your dealer or installation partner perform a compressed air measurement. These insights will help you to a setup that optimally follows the daily use. In a cascade setup you save considerably on energy consumption by switching multiple compressors with a lower capacity. The supporting compressors are only switched on when a peak demand occurs. They are off for the rest of the day, so they don't require any energy. A huge energy saving that will benefit your energy bill.
The cascade control divides the necessary running hours evenly over the various machines. This means you spread the load on your compressors.
An additional advantage is that you always have a backup compressor in case of maintenance, so that your production process continues without any problems.
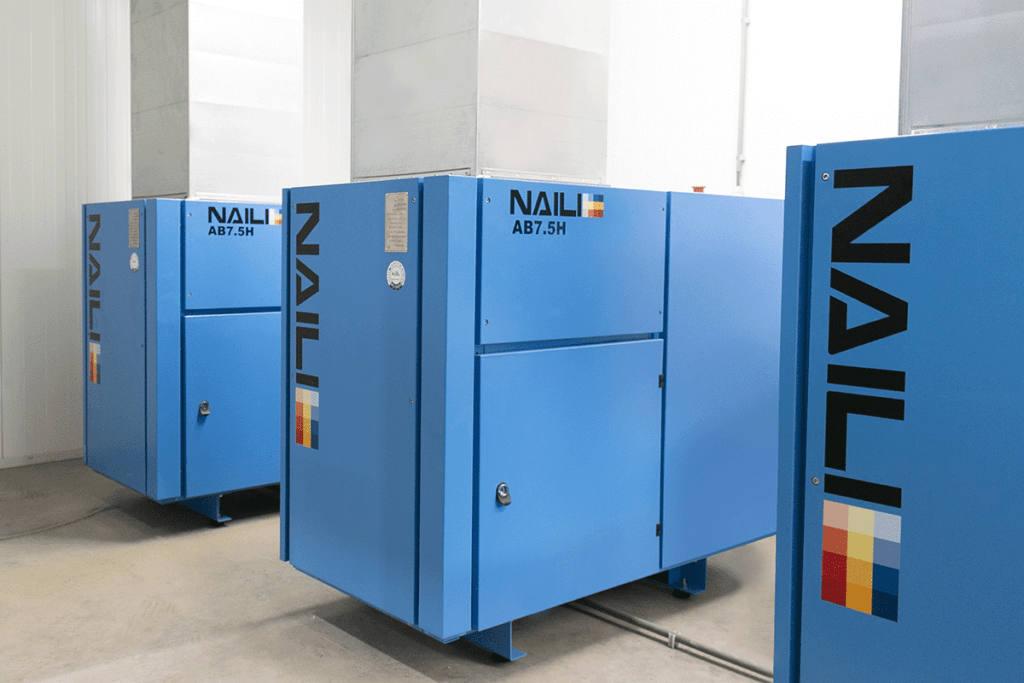
Your benefit: Reliable No damage to the rotating parts Extremely quiet
Rotary vane compressors
An extremely simple and reliable technique is used in a rotary vane compressor. You may know it from a vacuum pump. An electric motor is connected in-line to a rotor in which (steel) vanes are placed. The rotating movement of the rotor pushes the vanes outwards.
The rotor is eccentrically placed in the housing and ensures that the vanes form chambers around the rotor. As the chambers are reduced, pressure builds up.
Oil provides lubrication, cooling and sealing. It is therefore very important that you keep the oil in the right condition, as with any oil-containing machine.
The linear connection between motor and rotor ensures that there is no lateral load on the bearing. As a result, there will be no damage to the rotating parts. Naili limits your maintenance to the replacement of filters and oil. This makes this type of compressor very attractive to the user.
Moreover, this technique ensures that these compressors are very quiet in use. This allows you to place these compressors close to a workplace.
Performance
A rotary vane compressor has a very efficient energy transfer with low resistance because no energy is lost in V-belt or gearbox transmissions.
This provides energy savings of up to 20% compared to other common technology on the market. A lifetime of 70,000 operating hours is no exception for a vane compressor.
100% effectiveness due to frequency control (VSD)
Compressed air is expensive because over 85% of the used electrical energy is converted into heat and only 15% into compressed air energy. In addition, the higher the pressure, the more energy is required. Each additional bar of pressure that your compressor has to generate will cost you 7% more energy.

That is exactly why it is important to take a good look at the correct and most optimal use of the energy absorbed. From an energy point of view, it is most efficient if a compressor is switched off when the operating pressure is reached. However, in practice an on/off control is often not possible. Due to a too narrow pressure range, the compressor will switch too often, causing the motor to wear too hard.
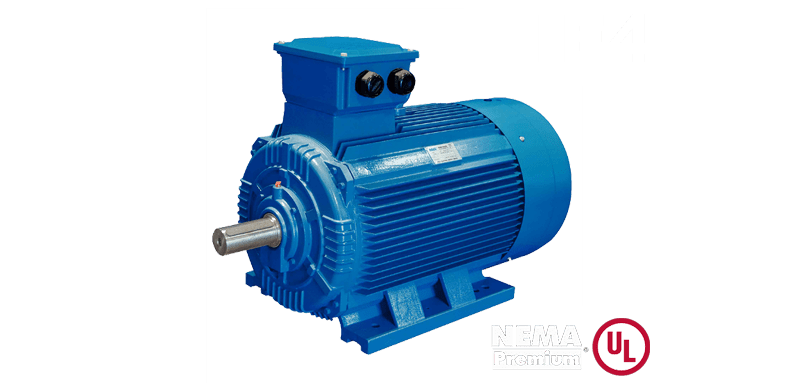
For that reason it is desirable that the motor adjusts its speed to the demand, so that it does not have to switch on/off every time the compressed air consumption does not require 100% power. As a result, the need to set overpressure in the system to accommodate fluctuating demand is no longer relevant. The speed will be increased when the pressure in the system decreases. The control of a frequency-controlled compressor keeps the pressure at the set desired pressure through PID calculations, making increased energy consumption due to overpressure a thing of the past.