Industry
simple and reliable technology
Rotary vane compressor for industry
Compressed air is essential to the industry. Your process depends on it. A reliable and efficient system should therefore not be missing in your business process.
An extremely simple and reliable technique is used in a rotary vane compressor. You may know it from a vacuum pump. An electric motor is connected in line to a rotor in which (steel) vanes are placed. The rotating movement of the rotor pushes the vanes outwards.
The rotor is placed eccentrically in the housing and allows the vanes to form chambers around the rotor. Because these are reduced, pressure can be built up. Oil provides lubrication, cooling and sealing. It is therefore very important, as with any oil-containing machine, that you keep the oil in the right condition. Due to the linear connection there is no lateral load on the bearing. This contributes to the fact that there is no damage to the rotating parts to be expected; which is a major cause of malfunctions with other types of compressors. As a result, the maintenance of a rotary vane compressor is limited to replacing filters and oil, which makes it very attractive for the user.
The use of this technology also ensures that a rotary vane compressor is very quiet in use.
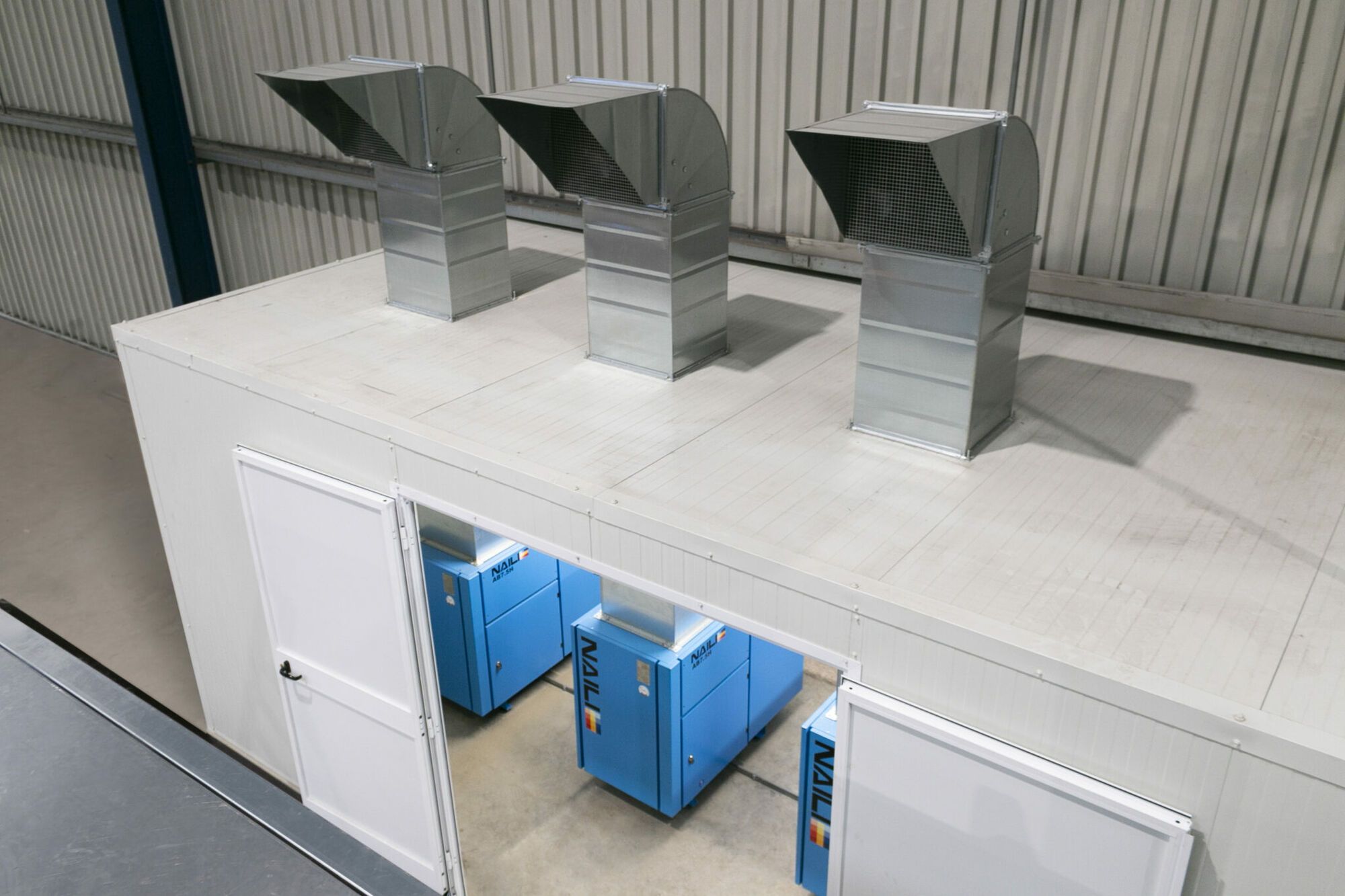
Rotary vane compressor performance
A rotary vane compressor has a very efficient energy transfer with a low resistance. This compressor gives you energy savings of up to 20% compared to other compressors. This is because no energy is lost in transmissions with V-belts or gearboxes. A service life of 70,000 operating hours is no exception for a vane compressor.
TCO (Total Cost of Ownership)
Compressed air is expensive because over 85% of the used electrical energy is converted into heat and only 15% into compressed air energy. In addition, the higher the pressure, the more energy is required. Each additional bar of pressure that your compressor has to generate will cost you 7% more energy.
That is exactly why it is important to take a good look at the correct and most optimal use of the energy absorbed. From an energy point of view, it is most efficient if a compressor is switched off when the operating pressure is reached. However, in practice an on/off control is often not possible. Due to a too narrow pressure range, the compressor will switch too often, causing the motor to wear too hard.
For that reason it is desirable that the motor adjusts its speed to the demand, so that it does not have to switch on/off every time the compressed air consumption does not require 100% power. As a result, the need to set overpressure in the system to accommodate fluctuating demand is no longer relevant. The speed will be increased when the pressure in the system decreases. The control of a frequency-controlled compressor keeps the pressure at the set desired pressure through PID calculations, making increased energy consumption due to overpressure a thing of the past.
A PB-series compressor is designed to meet this demand.
TCO (Total Cost of Ownership)
Compressed air is expensive because over 85% of the used electrical energy is converted into heat and only 15% into compressed air energy. In addition, the higher the pressure, the more energy is required. Each additional bar of pressure that your compressor has to generate will cost you 7% more energy.
That is exactly why it is important to take a good look at the correct and most optimal use of the energy absorbed. From an energy point of view, it is most efficient if a compressor is switched off when the operating pressure is reached. However, in practice an on/off control is often not possible. Due to a too narrow pressure range, the compressor will switch too often, causing the motor to wear too hard.
For that reason it is desirable that the motor adjusts its speed to the demand, so that it does not have to switch on/off every time the compressed air consumption does not require 100% power. As a result, the need to set overpressure in the system to accommodate fluctuating demand is no longer relevant. The speed will be increased when the pressure in the system decreases. The control of a frequency-controlled compressor keeps the pressure at the set desired pressure through PID calculations, making increased energy consumption due to overpressure a thing of the past.
Extra energy savings and backup through cascade setup
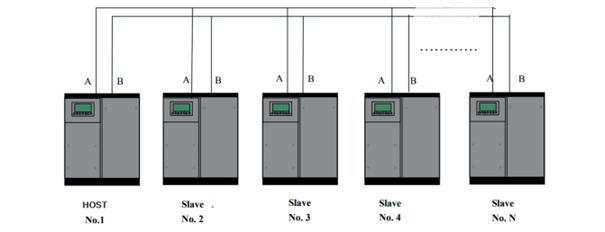
It is cost-effective to connect several compressors in a communicating setup. Therefore it is important to understand what volume and pressure of compressed air is required in a certain period of time. Always have your dealer or installation partner perform a compressed air measurement. These insights will help you to a setup that optimally follows the daily use. In a cascade setup you save considerably on energy consumption by switching multiple compressors with a lower capacity. The supporting compressors are only switched on when a peak demand occurs. They are off for the rest of the day, so they don't require any energy. A huge energy saving that will benefit your energy bill.
In order to evenly distribute the load on the compressors, the cascade control will ensure that the necessary operating hours are evenly distributed over the various machines.
An additional advantage is that you always have a back-up compressor in case of maintenance, so that your production process continues without any problems.